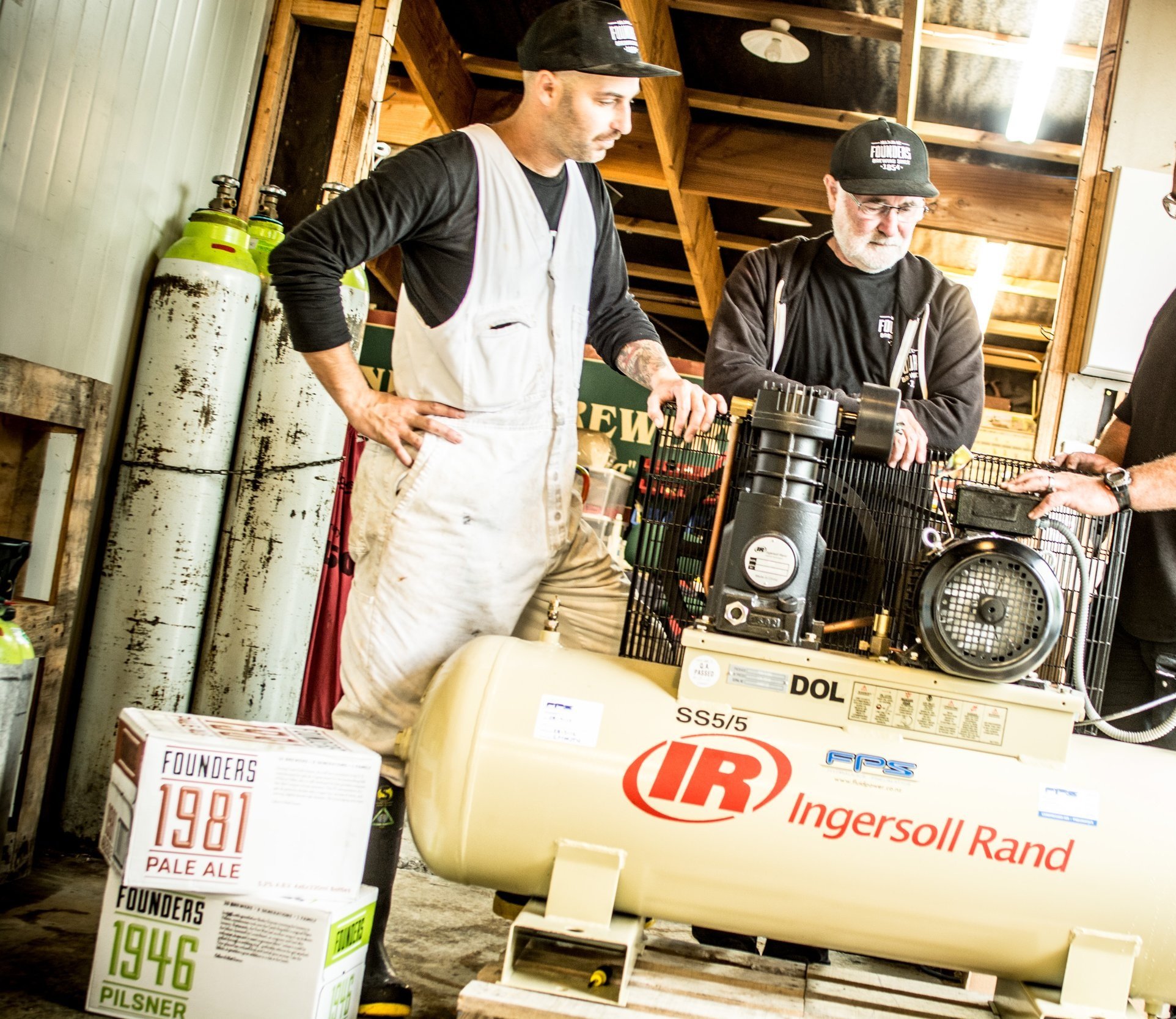
New compressor gives life to old keg washer
“FPS has always provided us excellent customer service. They maintain some of our key brewing machines. I always find them responsive and knowledgeable and up to the challenge to solve any problem we put to them.”
“FPS has always provided us excellent customer service. They maintain some of our key brewing machines. I always find them responsive and knowledgeable and up to the challenge to solve any problem we put to them.”
You wouldn’t think the machine that washes kegs would be so critical to operations at the iconic Founders Brewery in Nelson.
“We’ve had quite a challenge with our keg washer in the last couple of years,” says Matt Duncan, Head Brewer and member of the historic family that has owned Founders Brewery since 1854. “It finally got to the stage where we needed a serious solution.”
The keg washer frustrated everyone at the brewery. Matt says, “It would shut down every couple of hours each day and keeping up with demand was becoming a problem.”
During the busiest times of the year, the brewery ships about 100 kegs of fresh beer each week. It also receives about 150 kegs into the brewery for cleaning and refilling. Dirty kegs need to be cleaned and sterilised before they can be refilled and distributed around New Zealand. But the keg washer wasn’t doing its job.
“We were having to shut down the washer more and more often as the work load increased, so we called the team at FPS to help diagnose the problem.”
Founders Brewery already had a relationship with FPS.
“FPS supplies the hoses we use to brew and transfer beer. They provided us excellent customer service. They line up everything we need to change the hoses quickly so we have minimal disruption to operations.
“They also serviced the keg washer for a couple of years, helping it to stay running. I knew I could call them in to find out what was going on.”
John Bailey, the Air Division Compressed air/Pneumatics technician at FPS, pegged the problem straight away. The keg washer was in good nick, but the compressor was vastly under capacity and unable to keep up with production demands.
“John told us the compressor was not always opening the valves to allow water to flow in and out of each keg during the wash cycle. He recommended a new Ingersoll Rand piston compressor with SMC filtration. It has a huge capacity, which is ideal for future-proofing the business.
“Now, we wash as many kegs each day as we need to. The machine operates all day long without interruption. We can fill clean kegs right away and get the beer onto the truck, out the door, and into the market. And we get to spend more time brewing, which is what we are good at.”
Since FPS replaced the compressor, the keg washer has operated without issue.
“Even though it’s been functioning perfectly, John comes by to check on it every now and then. But I think he’s really here more for the beer.”