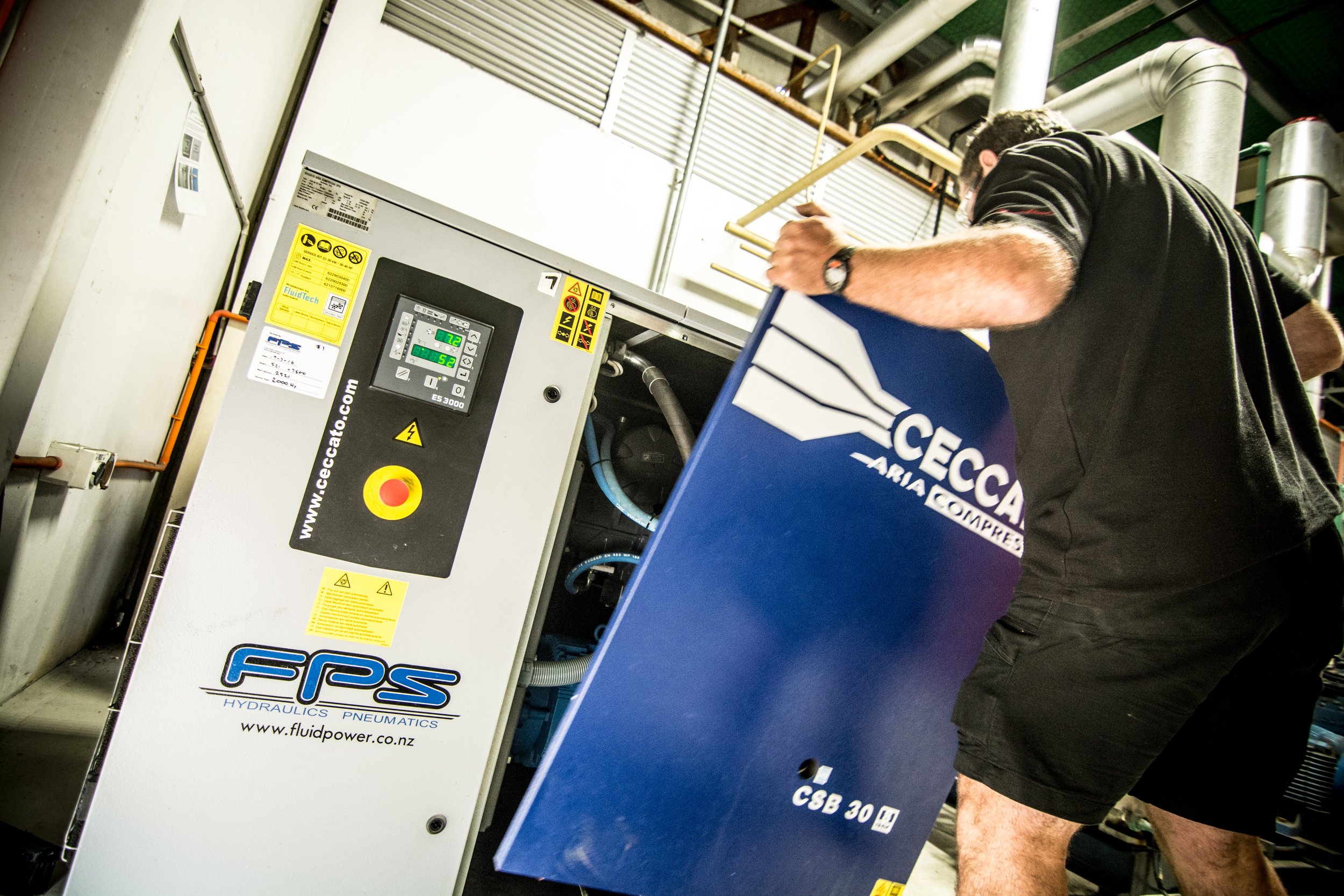
Talleys' relies on FPS' air team to ready their ice cream for export
Mike rates the experience of the FPS team highly. “I’m always confident in what they are doing and that they know their stuff.”
Mike Elston, Ice Cream Manager with Talley's Group Limited
Mike rates the experience of the FPS team highly. “I’m always confident in what they are doing and that they know their stuff.”
Mike Elston, Ice Cream Manager with Talley's Group Limited
Mike Elston, Ice Cream Manager with Talley’s Group Ltd, says their wet environment in Port Motueka used to present challenges for production of their ice cream until FPS sorted out a new compressor upgrade three years ago.
“The Port is wet, the factory is wet, and we have ongoing wash down requirements where all our equipment gets cleaned frequently. Everything gets wet all the time,” Mike says.
“We’d get this build-up of rusty gunk in our 20-year-old compressor lines that we’d have to clean out,” he says. “It caused issues with all the components in the system. It was just a mess and it was getting expensive to replace parts.”
Mike called in the FPS Air Team, led by Services Manager Chris Gray. They installed a new ring main air system, two rotary screw compressors, an air dryer, an air receiver, an activated carbon filtration system, and a stand by piston compressor to perform the lower-powered night duties.
“Now, you can go outside and open any water trap on the airline and you won’t find water in the system at all,” Mike says.
Since installation, the Air Team has been servicing the machines every 2,000 hours, as well as many of the pneumatic components within the system.
“We had a minor issue awhile back where the compressors were going out on high pressure alarm – they were going up to 9 bar when they should have cut out at 8 bar. Chris and John came out right away. John spent the whole day here watching the machine to see what happened when it reached the high-pressure state to isolate the issue. He was able to sort and fix it within the day.”
Mike rates the experience of the FPS team highly. “I’m always confident in what they are doing and that they know their stuff.”
He says it was the back-up service that won FPS the work in the first place. “The service they have given us is second to none. It’s excellent. If ever there’s a problem, Chris or John are over here almost at the drop of a hat.”
In fact, the change to the factory environment becoming more dry has had other cost-saving benefits for Talley’s as well.
“We used to have trouble with all of our valves and actuators. We’d have to replace them with new units and this started getting pretty expensive. Thanks to the work from FPS, we’ve not had to replace any in the last three years.”